Citadel's swords are hand crafted using old world techniques to produce some of the most unique and collectible samurai swords available anywhere. And while their methods may seem crude, the result is anything but. See below what is involved in the crafting of a Citadel Katana.
Citadel Samurai Swords List
The Blade and Polish
Citadel's katana blades begin life as billets of imported (European) 1075 high carbon steel. 1075 is a high carbon steel with just the right amount of carbon to make the blade's edge sufficiently hard but not too much as to risk becoming brittle.
The blades are heated in a coal fire and forged by hand hammering into the basic shape needed for that particular sword. The blade is then prepped appropriately, coated in clay and precisely heated to the critical temperature for the differential hardening quench. As any smith will tell you this is the "moment of truth" in crafting a samurai sword, as the quenching process puts the blade under tremendous stress. A crack or further flaw in the blade will produce an audible ping that will force the blade into the scrap bin. With a successful quench the blade is then de-scaled and any warps or bends are straightened and the final curvature (sori) adjusted as necessary. The blade is then tempered to it's final hardness.
At this stage the blade is polished by hand using a mix of natural and synthetic stones and powders in the traditional manner, progressing from the foundation polishing stones (arato) up to the final polishing paste/powder (Nugui) . Here is the sequence Citadel uses for each katana blade:
- synthetic stone "arato"
- natural stone "chu nagura"
- synthetic stone "koma-nagura"
- natural stone "uchigomori"
- final polish with "hazuya" stone and "nugui" paste/powder
This traditional polishing process produces a blade with a keen edge, clean lines, and flat surfaces not seen outside of high end custom swords or Japanese made blades.
Copper Habaki, Iron Tsuba and Fittings
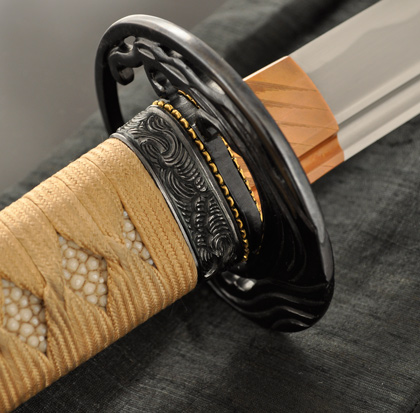
Once the blade has been polished it is time to fit the blade collar, or habaki. Typically cast brass, Citadel forges the habaki to each individual blade from solid copper for an exceptional fit. In addition a length of bronze is brazed along the cutting edge of the habaki to ensure that the blade will not separate the softer copper at this critical junction. The habaki is then filed to a final shape following the lines of the blade including the bo-hi if present. The habaki surface is finally polished and on the more elaborate swords a traditional scratch pattern engraved into the copper.
Following in the tradition of the artisans of old are Citadel's Tsuba and Fittings craftsmen. Lacking the equipment to cast large metal pieces means that each of the Tsuba, Fuchi and Kashira are cut and engraved by hand of pure iron (unless otherwise noted). Iron takes a beautiful patina and is subsequently resistant to rust though an occasional cleaning and light oil coating is recommended. In addition it is an extremely tough material and if ever subjected to tremendous shock will bend instead of break, a feature that any samurai would truly appreciate.
After the initial shaping of the piece Citadel's artisans use jewelers files, chisels, engravers, etc. to mold and shape the fitting into an interpretation of a classic Japanese style. This leaves each piece slightly unique although the overall impression is always the same; one of obvious skill and artistry. Even the simpler forms as seen in the Lotus Katana exhibit a sheer beauty in their execution.
Tsuka and Saya - Bringing it all together
Once all of the metal pieces are completed and fit to the sword work on the handle (tsuka) and scabbard (saya) may begin.
For the tsuka the wood core is carved and fit to the tang of the blade as a friction fit with the added security layer of a properly tapered bamboo pin (mekugi). Once the outer wood of the core has been shaped the handle is wrapped completely in a single high quality ray skin. The skin is processed at the forge, where they occasionally purchase rays from the local fisherman allowing them to select the finest skins available. This full same-gawa wrap hardens and strengthens the handle much more than is possible with the usual strips of ray skin panels. The seam is hidden under the tsuka-ito.
Wrapping the tsuka is a true skill and an art unto itself with many considerations to ensure a long lifetime of use. First strips of paper are placed at the top and bottom of the tsuka to help hold the ito in place. Small pieces of the proper paper are prepared by folding into small triangles that help the ito maintain its characteristic diamond pattern. Once ready the entire handle is tightly wrapped with imported Japanese Silk Ito, the highest quality ito available anywhere.
Similarly the saya is individually carved to match it's blade, ensuring a proper fit. Once shaped buffalo horn koiguchi, kurikata and kajira are precisely fit to the saya. The koiguchi in particular takes up to 8 hours of hand carving and shaping to complete per saya. Finally the saya is lacquered in several layers and buffed to a semi-gloss finish.
All of this hand work makes for some of the best fit and finish off the shelf available anywhere.
Citadel Samurai Swords List
Citadel Swords Production Video
Below is an older production video of the Citadel forge in action. Some processes have changed since the making of this piece (such as the full same-gawa wrap) but will give you a good general idea.